Recubrimientos en polvo de curado UV y tecnología de curado LED
Productos Revista Finishing Marzo 2019
Autor: Michael Knoblauch, presidente de Keyland Polymer Material Sciences.
El curado UV de revestimientos es una tecnología probada y ofrece una alternativa práctica y rentable al curado tradicional.
La luz ultravioleta (UV) se utiliza para curar revestimientos desde hace más de 30 años, y las empresas llevan más de 20 utilizando con éxito revestimientos en polvo curados con UV. Los recubrimientos en polvo de curado UV pueden sustituir al recubrimiento líquido con disolventes (en algunos casos, al recubrimiento en polvo termoestable) y son un material de acabado de interés para muchos materiales y productos nuevos.
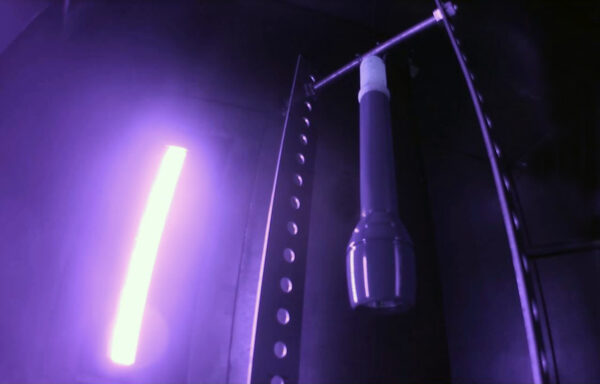
Las lámparas UV de alta potencia son la fuente de energía de la luz de curado, y las lámparas de arco o de media presión dominan el mercado.
Las lámparas UV de alta potencia son la fuente de energía de la luz de curado, y las lámparas de arco (o de media presión) dominan el mercado. En los últimos cinco años, los fabricantes de lámparas han desarrollado y están produciendo lámparas de diodos emisores de luz (LED) UV con una mayor producción de energía UV. Éstas están sustituyendo a las lámparas de arco y de media presión, y algunas están especificadas para su uso en nuevos sistemas de acabado.
El curado UV es muy diferente de los sistemas de curado por aire seco o térmico (calor). Es importante entender la curación y saber cómo evaluarla. El curado es una reacción química que tiene lugar en el interior del revestimiento y se mide por el número de cadenas de oligómeros reticulados o dobles enlaces totalmente reaccionados que quedan en la matriz del revestimiento tras la exposición al sistema de curado. Los tipos de sistemas de curado son el ambiente o «secado al aire», la energía térmica-calor o la exposición a la luz ultravioleta. La calorimetría diferencial de barrido (DSC) es un método fiable y repetible para medir el curado de un sistema de recubrimiento. Los usuarios suelen utilizar una prueba con disolvente MEK para evaluar el curado. Las investigaciones muestran que esta prueba puede producir resultados falsos negativos y falsos positivos.
Los líquidos y recubrimientos en polvo curables por UV son materiales fotopolimerizados con un fotoiniciador químico que responden instantáneamente a la energía de la luz UV, iniciando la reacción que conduce al curado. Para curar un revestimiento en polvo UV, una etapa de fusión separada precede a la etapa de curado, que suele durar 1-2 minutos o más, dependiendo del sustrato. El curado UV es casi instantáneo. Al considerar los revestimientos curados por UV para líquidos o polvos, es necesario equilibrar los parámetros de funcionamiento del sistema de revestimiento, la velocidad del proceso y el material de revestimiento con la gama espectral de la bombilla UV y la salida de energía del sistema de lámparas. Si la potencia espectral de la bombilla no coincide con la gama de absorción del fotoiniciador o si el sistema de lámparas no tiene potencia suficiente, es posible que el revestimiento no se cure completamente.
Restricciones reglamentarias y medioambientales
El interés de los consumidores por los materiales respetuosos con el medio ambiente (así como las normativas de salud y seguridad que eliminan o reducen la cantidad de materiales peligrosos) están cambiando la forma de fabricar los recubrimientos y de utilizar y aplicar los productos químicos. Las opciones alternativas del usuario son los barnices al agua; los barnices líquidos sin/con bajo contenido en disolventes y de curado UV; y los barnices en polvo termoendurecibles y de curado UV. El recubrimiento al agua es el sector de la industria de recubrimientos que crece con mayor rapidez. El agua está sustituyendo a los disolventes en pinturas y revestimientos. Además del reto de ser un sustituto de calidad y rendimiento 1 a 1 de los recubrimientos con disolventes, los recubrimientos al agua tienen unos costes económicos, sociales y medioambientales que aún no se han medido del todo. El agua es un recurso natural escaso y desigualmente distribuido.
Los recubrimientos en polvo de curado UV tienen muchas ventajas operativas: reducen el consumo de energía y el sistema de aplicación total ocupa menos espacio en la planta, aumenta la productividad, reduce el uso de materiales y produce mayores beneficios por hora. Además de estas ventajas operativas, los recubrimientos en polvo de curado UV presentan beneficios para la salud, la seguridad y la normativa. Al ser 100% sólidos, no contienen disolventes ni agua. No tienen sustancias químicas peligrosas o reguladas y no requieren permisos para su fabricación o uso. Cuando se tienen en cuenta en un modelo de coste total aplicado, estas ventajas convierten a los recubrimientos en polvo de curado UV en una buena inversión. El gráfico 1 muestra las ventajas de productividad del recubrimiento en polvo de curado UV en comparación con los recubrimientos líquidos y en polvo termoendurecibles. Cada barra es la suma del tiempo necesario para completar la aplicación hasta el curado.
Los recubrimientos en polvo de curado UV y los recubrimientos en polvo térmicos se hacen igual. La diferencia es la resina UV, que está específicamente diseñada para curarse con luz UV. Los tipos de resina típicos son los poliésteres, los epoxis y los uretanos. Los aditivos y pigmentos (junto con el fotoiniciador) se añaden a la resina y completan la formulación. La única diferencia entre los recubrimientos en polvo térmicos y los curados con UV es la separación de una fase continua de calentamiento para fundir y curar en una fase corta de calentamiento para fundir y seguida de una fase casi instantánea de curado con UV. El gráfico 2 es un ejemplo de las diferencias de tiempo y temperatura entre un recubrimiento en polvo térmico de cocción ultrabaja (ULB) y un recubrimiento en polvo de curado UV para el acabado de tableros de fibra de densidad media (MDF). El polvo ULB tiene un tiempo de fusión∕curado de 5 minutos a 130 C, con un tiempo de inicio a fin de unos 32 minutos. El polvo curado con UV se introduce en el horno durante un minuto calentado a 110 C, seguido de un curado UV casi instantáneo. El tiempo total en línea de principio a fin es de 20 minutos.
Tecnología de curado por luz UV
La potencia de la lámpara UV se describe como irradiancia (intensidad), y la potencia de la lámpara se mide a una distancia específica, con la notación mW∕cm². Al cambiar la distancia, cambia la irradiancia. El segundo descriptor es la exposición (densidad de energía), la cantidad de potencia de la lámpara que llega a la superficie del objeto que se está curando a medida que se desplaza por el campo luminoso de la lámpara; la notación es mJ∕cm². Al variar la velocidad de la línea, cambia la exposición. Es importante comprender cómo cambian las condiciones de curado al variar la potencia de la lámpara, la distancia y el tiempo.
La tabla 1 muestra los resultados de cuatro mediciones de tres tipos de lámparas: Lámparas de mercurio de presión media de 300 y 600 vatios y un LED 395, con potencias al 50% y al 100%. La tercera condición muestra dónde se realizó la medición en el espectro UV (UVV y UVA2). Las dos constantes para todas las pruebas son una distancia de 4 pulgadas y una velocidad de 5 pies por minuto.
El espectro de luz ultravioleta tiene tres bandas entre 100 Nm y 400 Nm. Los fabricantes de lámparas nombraron una cuarta banda UVV 400-450 Nm. Esta banda es importante porque la energía UV en este rango cura los recubrimientos gruesos, como los recubrimientos en polvo curados con UV. Las lámparas UV de arco y media presión emiten energía luminosa en las cuatro bandas UV y en luz visible por encima de 400 Nm. Dependiendo del tipo de lámpara, la irradiancia energética y la exposición variarán a lo largo del espectro. Los fotoiniciadores absorben la luz UV en diferentes longitudes de onda. Las longitudes de onda de emisión de la luz UV deben coincidir con las longitudes de onda de absorción del fotoiniciador para iniciar y completar la respuesta de curado en el revestimiento.
Curado por LED UV
El desarrollo y la comercialización de los LED UV es un avance reciente e importante en la tecnología de curado por luz UV. El arco UV y las lámparas de media presión son muy eficaces, pero tienen limitaciones. Son ineficientes desde el punto de vista energético; las bombillas emiten calor IR; con el tiempo la intensidad de la lámpara se degrada; están dopadas (mejoradas) con metales pesados para cambiar el espectro de irradiancia; y las grandes matrices requieren un sistema de refrigeración por aire de reposición y son difíciles de ajustar o montar en un robot. Los LED UV abordan muchas de esas limitaciones.
Las pruebas de DSC demuestran que un UVLED de 395 Nm curará un revestimiento en polvo transparente, negro, blanco y otros revestimientos en polvo de absorción UV, pigmentados y curados con UV no conflictivos. Los fabricantes de LED están aumentando la potencia de salida (intensidad) de los emisores LED UV, ampliando así las posibilidades de aplicación. Es posible montar un emisor LED UV en un robot para mover el emisor a zonas que de otro modo no se podrían curar porque el curado UV es por línea de visión. La superficie del objeto a curar debe «ver» la luz UV. El curado LED UV no está exento de desafíos. Se necesita más investigación y desarrollo para superar los conflictos de absorción de UV en pigmentos y fotoiniciadores.
El curado UV de revestimientos es una tecnología probada y ofrece importantes ventajas operativas, sanitarias, de seguridad y normativas, lo que convierte al curado UV en una alternativa práctica y rentable al curado tradicional. Los continuos avances en la tecnología LED UV están incrementando el mercado de los materiales de curado UV, en concreto los recubrimientos en polvo de curado UV. Las mejoras en los equipos de LED UV y los desarrollos químicos simultáneos de los recubrimientos en polvo de curado UV han convertido la combinación de LED UV y recubrimientos en polvo de curado UV en una tecnología de acabado habilitadora, no sólo para sustituir a los recubrimientos con disolventes, sino también para muchos nuevos materiales y mercados de productos.